Nearly 200 feet directly beneath downtown Columbus, Ohio is a massive new 4-1/2 mile, 20-foot diameter tunnel that collects storm water during heavy rainfall. As with Columbus, years ago storm water systems for most of the nation’s cities were designed to collect runoff from a 2-year event. So, when heavy rains occur, water collects in the streets and often strands vehicles, causes power outages and damages homes and businesses.
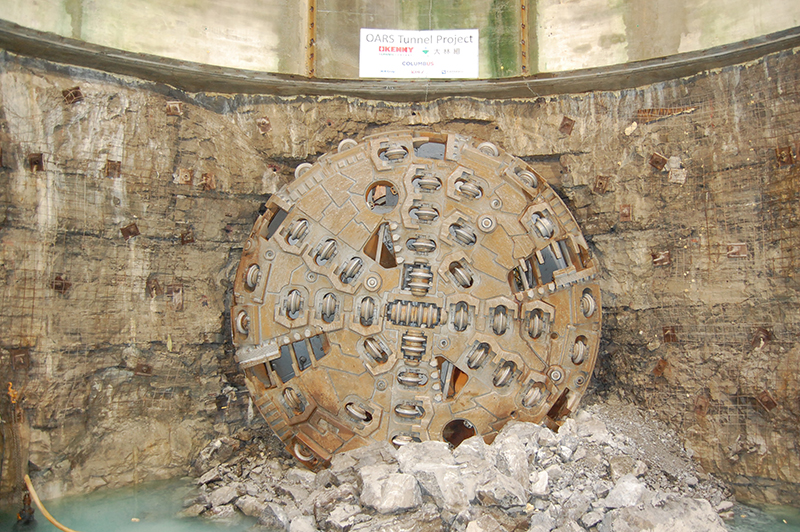
UNDERSIZED STORM WATER SYSTEMS
Columbus’ downtown main combined storm water and wastewater sewer system was built in the early 1930s with 13 combined sewer overflow points that discharged sewage into the Scioto River during heavy rainfall events. In 2004, the Ohio EPA issued a Consent Order requiring the combined sewer overflows to be adequately controlled by 2025. To address the order, the city originally planned to construct traditional, shallow open-cut sewer projects throughout the downtown in four phases from 2015 to 2025. However, DLZ came up with another solution – a massive tunnel beneath the city to collect the runoff and transport it to the city’s wastewater treatment plant. The tunnel would be large enough to meet the Consent Order by reducing combined sewer overflows up to a 10-year level of wet weather flow protection and would also be operational 8 years earlier than the original plan’s completion date of 2025. Columbus hired DLZ to develop the conceptual plans, design reports and construction plans and specifications for the tunnel. In addition, DLZ managed the design team, communicated with all the project stakeholders, and provided technical support during construction.
Named the Olentangy-Scioto River Augmentation and Relief Sewer Tunnel or OARS Tunnel, the massive tunnel passes under downtown Columbus, below buildings, bridges, interstate highways, railroads and the Scioto River.
ENGINEERING & CONSTRUCTION CHALLENGES
Building the tunnel was the best alternative but there were two significant project challenges that had to be addressed to be successful. First, a surge analysis study determined that rapid filling events could cause surge waves to propagate into the upstream collection systems, either causing overflows into the streets or causing damage to the existing system. Typical practice to correct these surges is to use gates to control inflows or to provide additional surge storage. However, DLZ took an innovative approach to design surge control storage directly into the six drop shaft structures that lead down to the tunnel.
Massive surge relief chambers and ventilation outlet structures were designed into the inlet shafts to protect the sewer system from pressure waves and air entrapment during tunnel filling that could lead to sewage geysers. A surge analysis helped to define the size and configuration of the relief structures at each of the six drop shaft locations. This method of eliminating surge waves had never been done before. Also, by designing the tunnel system to flow while fully surcharged maximizes the storage and flow capacity, and subsequently, maximizes the amount of storm water that flows to the wastewater treatment plant for purification.
The second challenge was related to construction. The tunnel was mined in karstic limestone with 50’ of rock cover. A positive feature of having the rock cover is that it prevented surface settlement; however, it was a very difficult geotechnical setting to mine due to the large quantities of groundwater flowing through the rock. In some cases, high pressure groundwater inflows exceeded 5,000 gallons per minute. Even more problematic was the fact the Tunnel Boring Machine (TBM) did not encounter isolated pockets of high groundwater inflow, but rather, almost continuous groundwater inflow along most of the tunnel alignment. Tunneling in this type of condition has only been performed on a few projects throughout the world.
To address this issue, muck handling was accomplished by pumping the rock slurry during the drilling process. And to cut off groundwater in order to gain access to the cutter face for maintenance and replacement of the rock cutters the contractor, Kenny/Obayashi Joint Venture, developed a “reverse-flow grout procedure”. Essentially, this procedure pumped feed water out of the front excavation chamber until the flow of water through the rock was going away from the TBM. Then, grout was introduced which naturally flowed into the openings and fissures in the rock where it sealed off the inflow of groundwater.
Another thing that made this project unique was that it was very rare that a TBM mining in rock would require the use of a pressurized cutting chamber. And even more rare was the fact the TBM had to mine in a slurry pressure-balanced environment. So, several features were designed into the TBM to give it as much flexibility as possible to increase production rates and successfully mine through rock that had near continuous, high-pressure groundwater inflows.
PROJECT BENEFITS
One major social benefit this tunnel project provides is the ability for Columbus to continue developing and growing its downtown area while protecting the Scioto River and the environment. In fact, most people working or living in the area of the project were not aware the tunnel was being constructing directly beneath them. The project also benefits a community of over 1 million people by addressing the Consent Order and bringing Columbus into compliance with the Clean Water Act. It’s estimated the new tunnel will redirect nearly 2 billion gallons of combined sewage overflows from the Scioto River to Columbus’ wastewater treatment plant annually. However, this estimate may be low. Last year alone, nearly 16 billion gallons of combined sewage was redirected through the tunnel and treated at the wastewater plant instead of overflowing to the Scioto River.
In addition, the project essentially eliminated the city’s 13 downtown combined sewer overflows and has allowed for the development of greenways and parks within the downtown area and helped transform the old riverfront area into vital public green space. The additional storage volume provided by the tunnel also eliminated the need for above ground storage for runoff and a future high-rate wastewater treatment system saving the city an estimated $175 million.
FUTURE OUTLOOK
Completed in July 2017, the OARS tunnel is now the backbone of the Columbus Wet Weather Management Plan. At a cost of over $370 million, it is the largest capital improvement project in the city’s history. Designing the downstream shafts to be open to the atmosphere and using odor control facilities at the upstream shafts allow for fresh air to flow through the tunnel. This allows the city to control odors and protects the concrete tunnel lining from corrosive gases that would otherwise build up in the sewer. Consequently, the expected design life for the tunnel exceeds 100 years.
Just two weeks after the tunnel was completed a major rain event hit Columbus filling the OARS tunnel and shafts to its maximum capacity and the system worked beautifully. The project also allows the city to implement a more robust storm water control system and connect future sewer extensions to the tunnel enabling the city to grow and develop.
As other cities address this same issue of undersized storm sewers and congested business districts, massive tunnels hidden beneath the cities are becoming a more and more feasible approach to collecting stormwater and complying with the Clean Water Act.